Common Cobot Safety Risks & Prevention Tips
Cobots are often touted for their safety features and ability to “collaborate” with humans. While it’s true that cobots can be safer than traditional industrial robots, that doesn’t mean they are risk-free.
We’ll look at what differentiates cobots from industrial robots, along with important safety considerations you’ll need to look for before implementing this innovative technology.
Cobots vs. Industrial Robots
In many ways, collaborative robots (cobots) are similar to standard industrial robots. They both move or assemble products and perform other material-handling functions. The key difference is that cobots are designed to be used near or in direct collaboration with humans. That is why cobots have force sensors to determine how much force should be applied to the mechanical parts of the robot.
In other words, a cobot can “feel” contact with a human, the workpiece, or another object.
Another defining difference between an industrial robot vs. cobot is that the cobot is designed to minimize pinch points. In a traditional robot, the articulating arms are connected to open joints or linkages that twist and turn at high speeds, posing safety hazards. The linkage assemblies on cobots are typically protected with sealed, rounded corners to enhance safety. The cobot cells also move at slower speeds to reduce the maximum force that can be applied to anything it comes in contact with, including humans.
Ultimately, you can program a traditional robot to function collaboratively with a human and achieve similar functionalities, but additional safety guards, fencing, and force sensors need to be engineered into the design, and it will need to be programmed to operate at reduced speeds.
Cobots are designed to be used near or in direct collaboration with humans
Examples of Cobots in Action
Manufacturers often consider cobots for tasks where a person will interact directly with the robot or peripheral equipment. Examples might include:
Palletizing
- A cobot might build one pallet while an operator exchanges another pallet. This allows continuous work without the robot needing to stop.
Assembly Assistance
- A cobot can hold parts in place for a human to assemble, such as adding screws or bolts. The cobot would then move the assembled components for further processing.
Machine Tending
- Cobots can load blanks into a CNC machine and then retrieve the finished products. This function is common in operations requiring repetitive and precise loading and unloading.
Labeling
- Cobots are often used to apply labels to products or pallets, moving slowly and safely.
Cobot Safety Risks
In general, cobots are relatively safe. But like any equipment with safety features, user error or a failure to follow safety protocols can result in injuries.
Likewise, poor planning and implementation or an improper safety system analysis can lead to issues. This is common for manufacturers that order a “standard” cobot from a distributor rather than working with an integrator that custom-engineers a robotic solution with the user and function in mind.
All that said, one of the biggest potential cobot safety risks doesn’t come from the cobot itself, but from the load that the cobot carries. The force sensors on a cobot detect whether it hits something and will stop, but the box or product held by the end-of-arm tooling will transfer or disperse the load at different ratios than the cobot itself and the sensors may not detect an issue, or it may delay slowing down or stopping.
All elements of a production line need to be evaluated in conjunction with the cobot to determine potential safety risks.
Cobot Safety Hazard Prevention Tips
When designing a safe cobot solution, the most important factors are weights and rates. What are you moving and how fast do you want to move it? Some material handling automation tasks simply aren’t suitable for cobots due to their mass or the rate at which they need to be assembled or moved down the line.
Assuming you have appropriate weights and rates, several cobot safety features can be implemented to help prevent injuries, including:
Area Scanners — Uses cameras/scanners that detect unusual movements at set distances from the cobot’s arm. When a person enters the restricted zone, the cobot will slow or stop.
Light Curtains — An invisible fence sends lasers to a reflector. When an unexpected object (like a human) breaks the beam, the cobot stops or slows down.
Fencing — A physical barrier placed at proper safety setbacks can prevent unauthorized entry.
Should Our Facility Implement a Cobot Solution?
Cobots are a relatively recent innovation in robotics, leading some manufacturers to believe they need the latest and greatest. They’re often marketed to smaller shops that haven’t used robots before because the software and interfaces are designed so that inexperienced operators can program the robot with minimal training.
However, it’s important to match the right solution to the task at hand and know the limitations.
For example, some manufacturers believe that cobots require fewer safety features or that they’ll take up less space. That isn’t always the case. Likewise, since they’re smaller, there’s a perception that they’re less expensive than traditional robots. Truth is, they’re usually comparable and sometimes even more costly.
To determine the proper solution, it’s ideal to work with a robotics professional to conduct a risk assessment. This is one of the most important safety steps taken in the early stages of development.
A robotics engineer can also determine the required setback distance calculations for any perimeter guarding and safety devices. A proper safety validation should also be carried out before turning the equipment over to the end user.
Here at QComp, ANSI and ISO standards play a role in ensuring we provide our customers with the safest solutions possible. We are bound by regulations enforced by OSHA and we also have a moral obligation to ensure those that use our equipment aren’t injured. Our team is A3 Certified, meaning we uphold the highest safety standards and stand behind our impressive safety record.
Want to explore whether a cobot or traditional industrial robot is the right solution for your material handling challenge? Contact our experienced team of engineers and integrators to talk through your needs.
Share this
You May Also Like
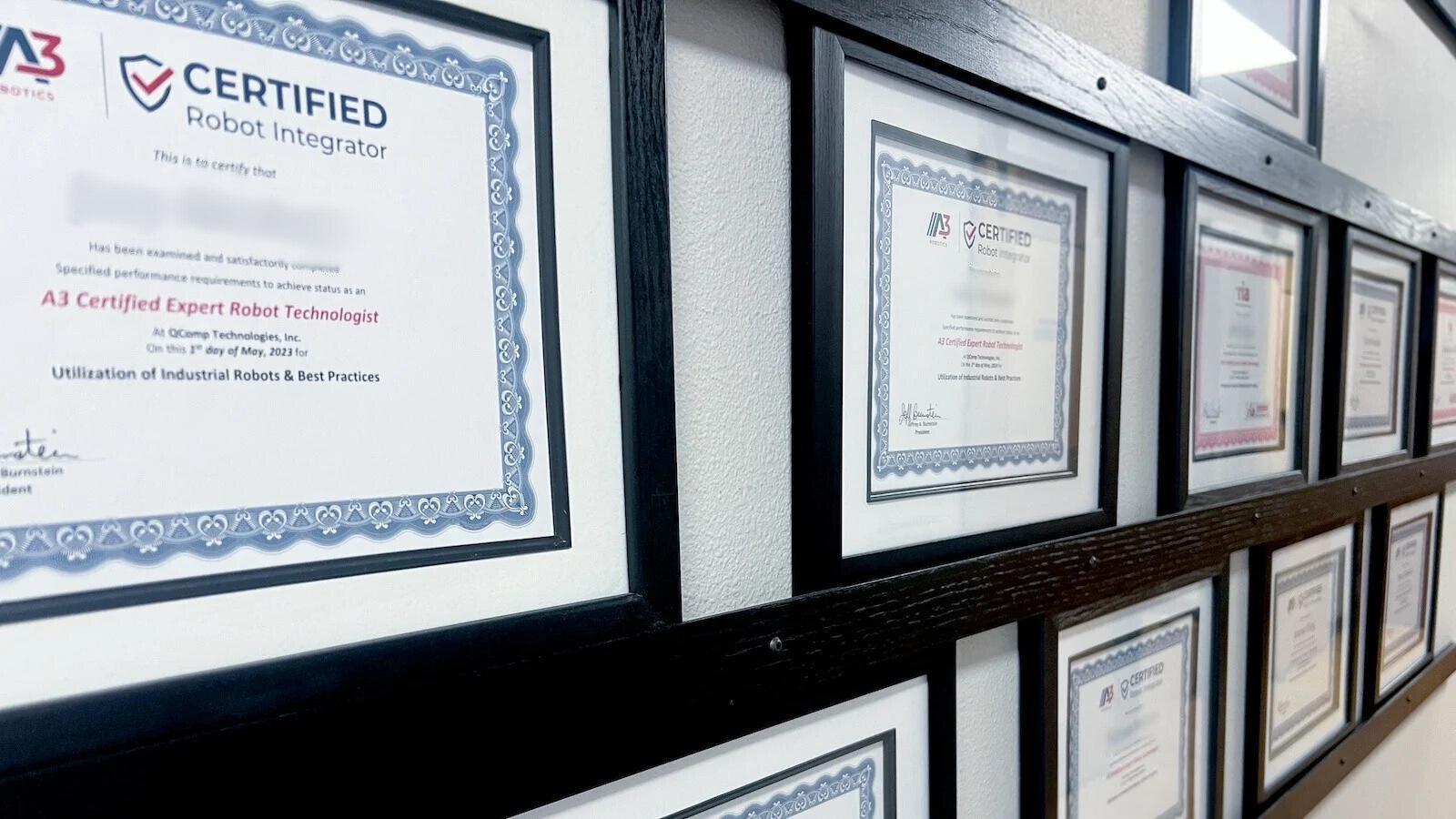
Why A3 Safety Certification Matters for Robotic Integrations
What is A3 safety certification? Explore the benefits and importance of The Association for Advancing Automation (A3) certification for robotic integrators.
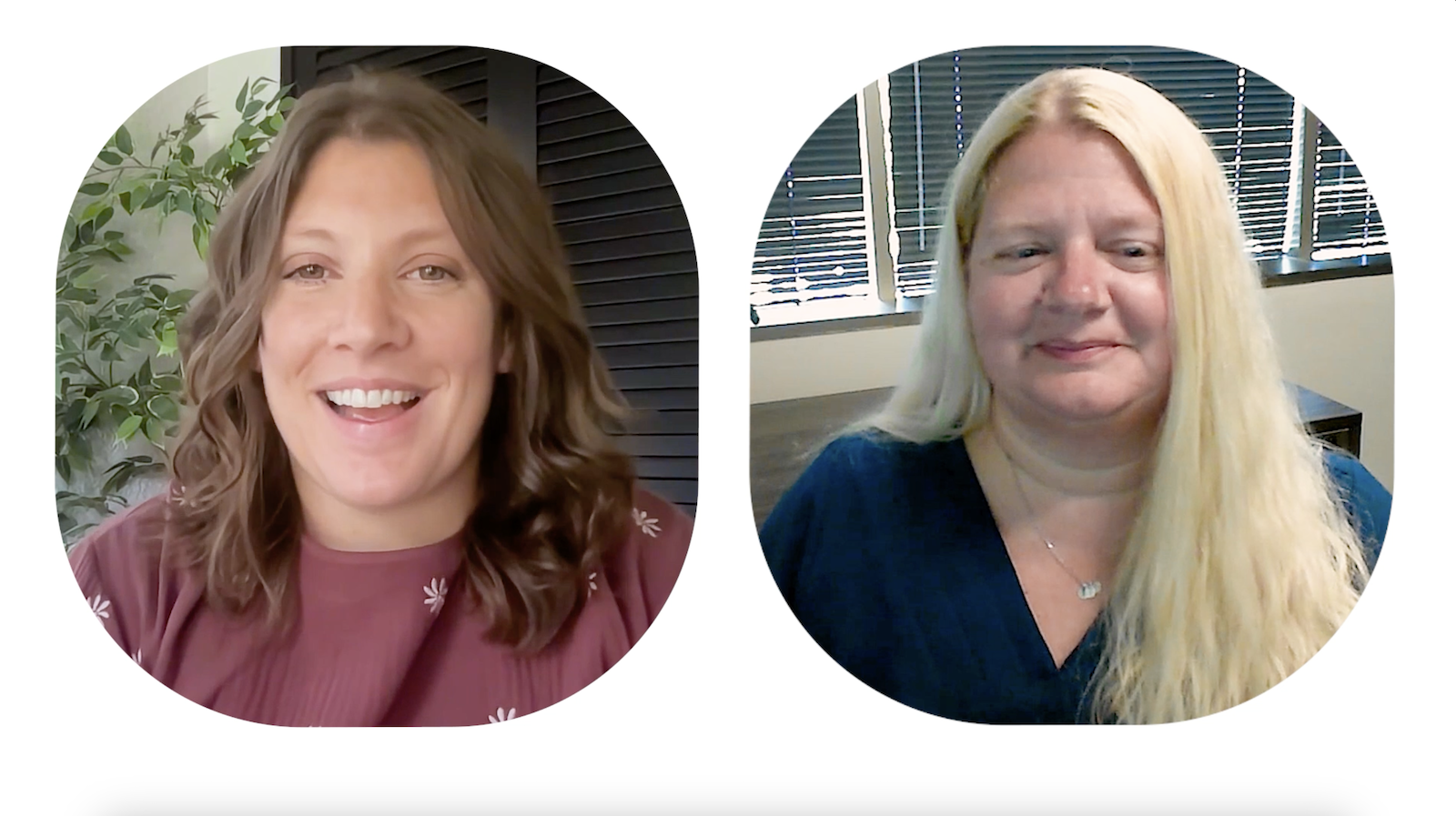
The Automation Advantage: Combat Labor Shortages and Win the Talent War
Discover how automation can help manufacturers tackle labor shortages, improve safety, and achieve a positive ROI in this insightful blog post conversation between industry experts.
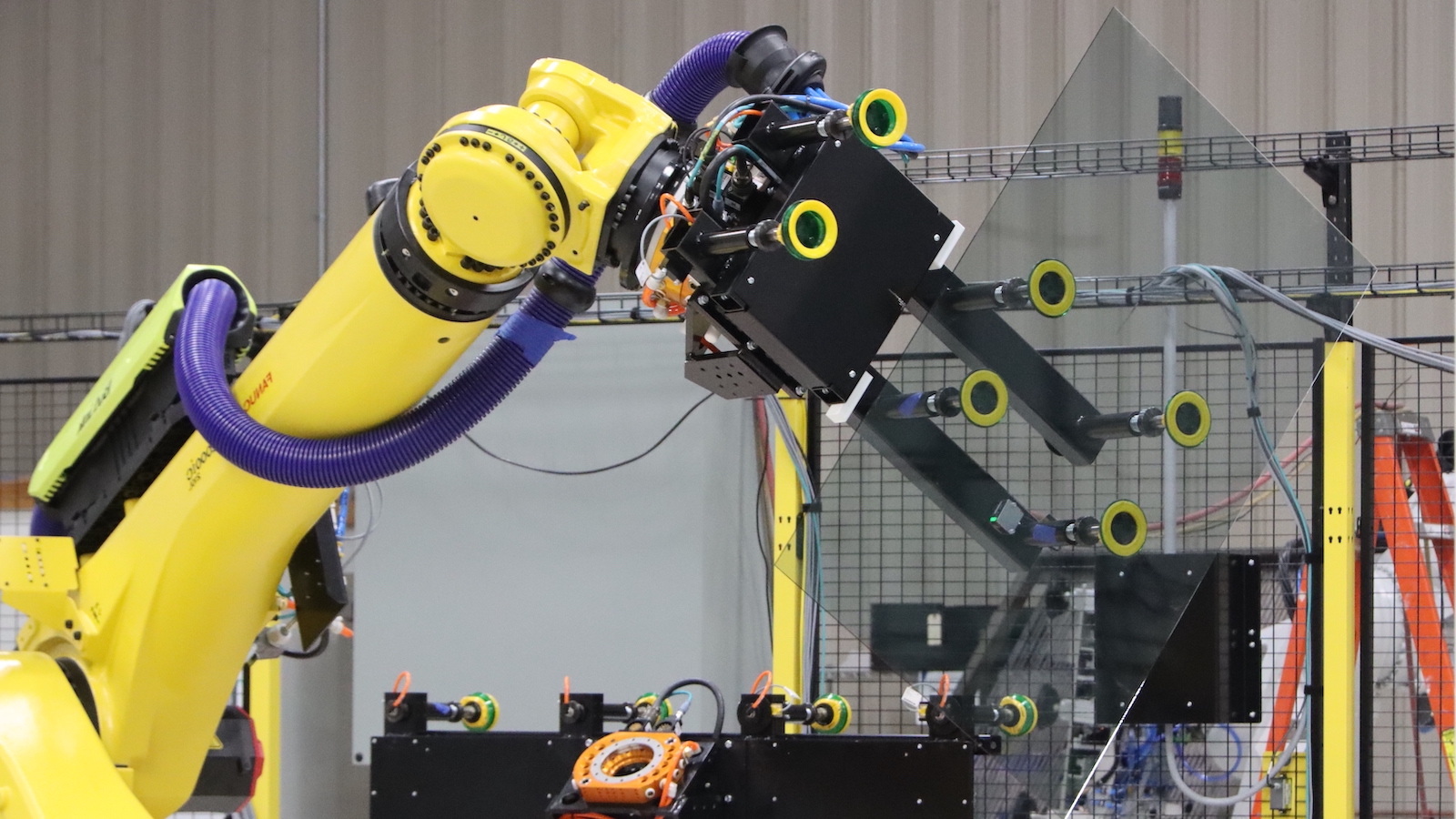
Improving Glass Industry Safety: How Automation Helps Prevent Injuries
How to improve safety in the glass manufacturing industry using robotic automation. Explore how a leading robotics integrator is solving the toughest challenges.