Why A3 Safety Certification Matters for Robotic Integrations
Safety. It’s the main reason why many manufacturers integrate robotics into their production lines and workflows. Integrating robots to perform the so-called 3Ds (dirty, dangerous, and difficult tasks) is proven to reduce the risks of ergonomic strains, musculoskeletal injuries, and injuries resulting from strenuous and repetitive motions.
As much as a robot can support safety initiatives, however, it can also be a major safety hazard if not properly programmed and tested. Just as crucial is proper training for those who work alongside robots and service them.
In fact, the Occupational Safety and Health Administration (OSHA) states that many robot accidents occur during maintenance, programming, setup, and other non-routine operating conditions.
If you’re a manufacturer that supports the highest safety standards, you’ll want to partner with a robotics integrator that shares those same values and backs it up with safety certifications from The Association for Advancing Automation (A3).
What is A3 Safety Certification?
Founded in 1974, The Association for Advancing Automation is the largest automation trade association in North America, providing education, information, and safety training for robotics integrators.
A3 developed a Certified Robot Integrator Program in response to an industry need for technical and robot safety benchmarks. Certification is granted only to those who successfully complete the A3 program and pass rigorous testing to demonstrate that they can deliver safe, reliable, and high-quality robotic systems and services.
Not all integrators are granted access to the certification program; they must first prove they have high levels of proficiency, experience, and success.
To qualify, a rigorous third-party audit is conducted to assess the robotic integrator’s processes across various departments, including project management, accounting, and more, and includes hands-on testing for robot engineers, technicians, and anyone who programs or works with robots. To maintain the certification, individuals must be audited every two years.
Robotic Safety Considerations for Manufacturers
Meeting safety standards not only helps ensure the physical safety of those who work around robots but also reduces liability risks. Furthermore, manufacturers that increase the number of accident-free days are more attractive to recruits, potentially helping to ease labor shortages. Safer equipment also leads to better productivity, less downtime, and improved morale among employees.
All that said, injuries from robots are relatively low nationwide and prevent innumerably more injuries than they may cause.
When an injury does occur, however, it is often serious because of the strength and speed of most robotic equipment. In particular, collaborative robots that directly interact and share workspaces with workers pose greater safety risks, stressing the importance of proper implementation and training.
Why Choose an A3 Robotics Integrator?
Manufacturers that place safety as their number one priority can’t risk their reputation on a robotics integrator that doesn’t share the same goals. While it’s critical for a robot to perform complex tasks and improve productivity and throughput, it can’t be done at the risk of lower worker safety.
QComp Technologies was among the pioneering integrators to pursue A3 certification back in 2012 when the program first was launched. To comply with A3 safety standards, our team hired a robotic cell safety trainer and implemented the necessary processes to ensure the well-being of both our employees and those who use our robotic solutions in the field.
Our reassurances go beyond a simple commitment to safety. The minimum requirement for certification is to provide a risk assessment. Our team takes it a step further and validates the safety of all electronics, controls, and components. As part of the verification process, we provide comprehensive documentation — sometimes exceeding 40 pages — outlining every safety point.
Such rigorous testing is not required for A3 certification, but we choose to provide it to ensure everyone’s safety. Once the robotic solution is installed, we provide rigorous training for end users to ensure they are confident using the equipment.
Of course, robots must complete the task at hand, and our engineers and technicians have designed some of the most complex robotic solutions imaginable for leading global brands. Want to talk through your automation challenges and how our team can support your safety and productivity initiatives in tandem?
Contact us to start the conversation.
Share this
You May Also Like
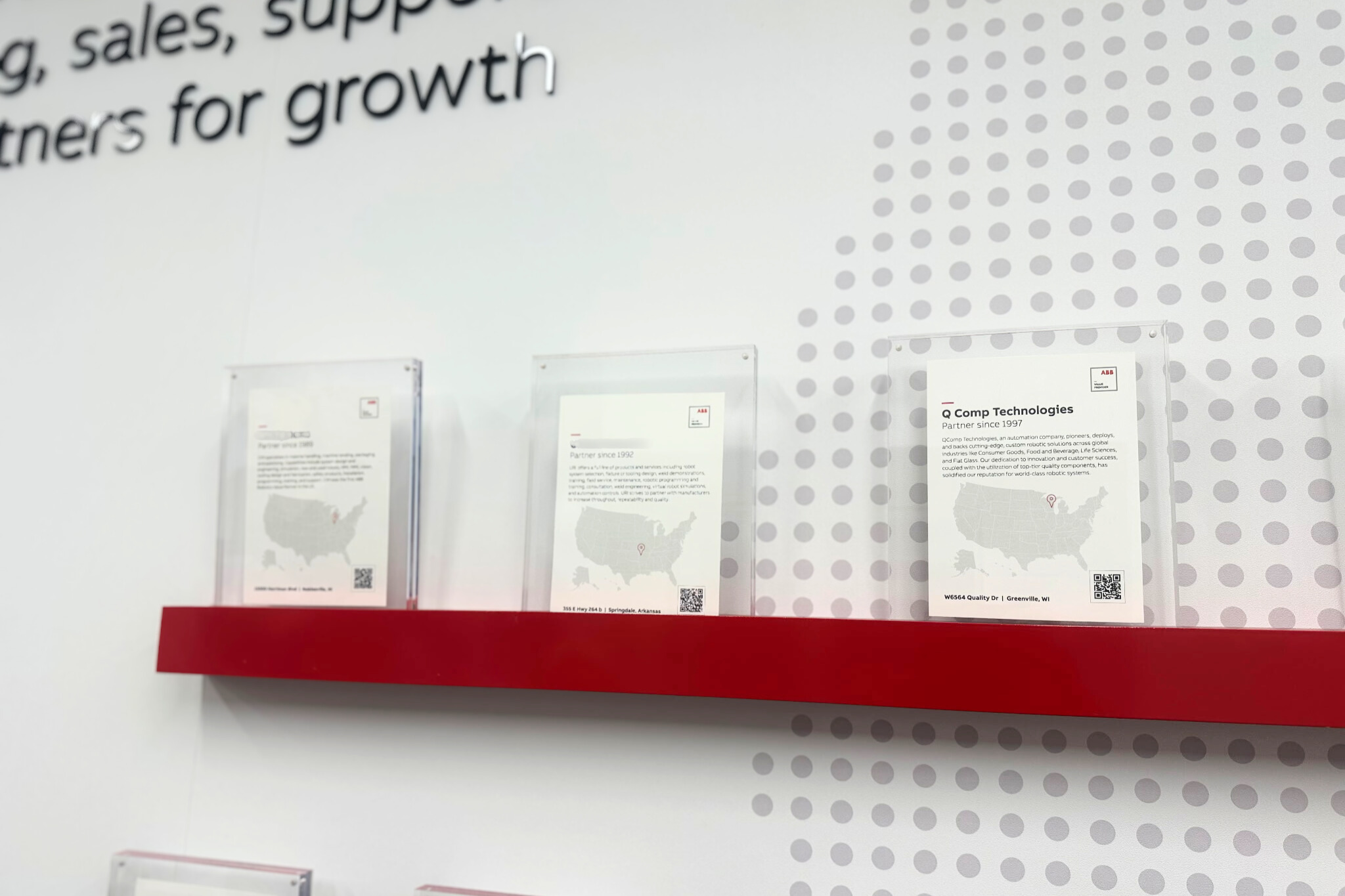
QComp: Proud to Be One of the First ABB Value Providers in the World
QComp was the third company in the world to join ABB’s Value Provider Program. Discover how decades of partnership and proven expertise help us deliver smarter, certified automation solutions that conquer complexity.

What Is Proactive Development of Robotic Solutions?
What is the proactive development of robotic solutions for complex material handling challenges in manufacturing, and what are its benefits? Learn more.
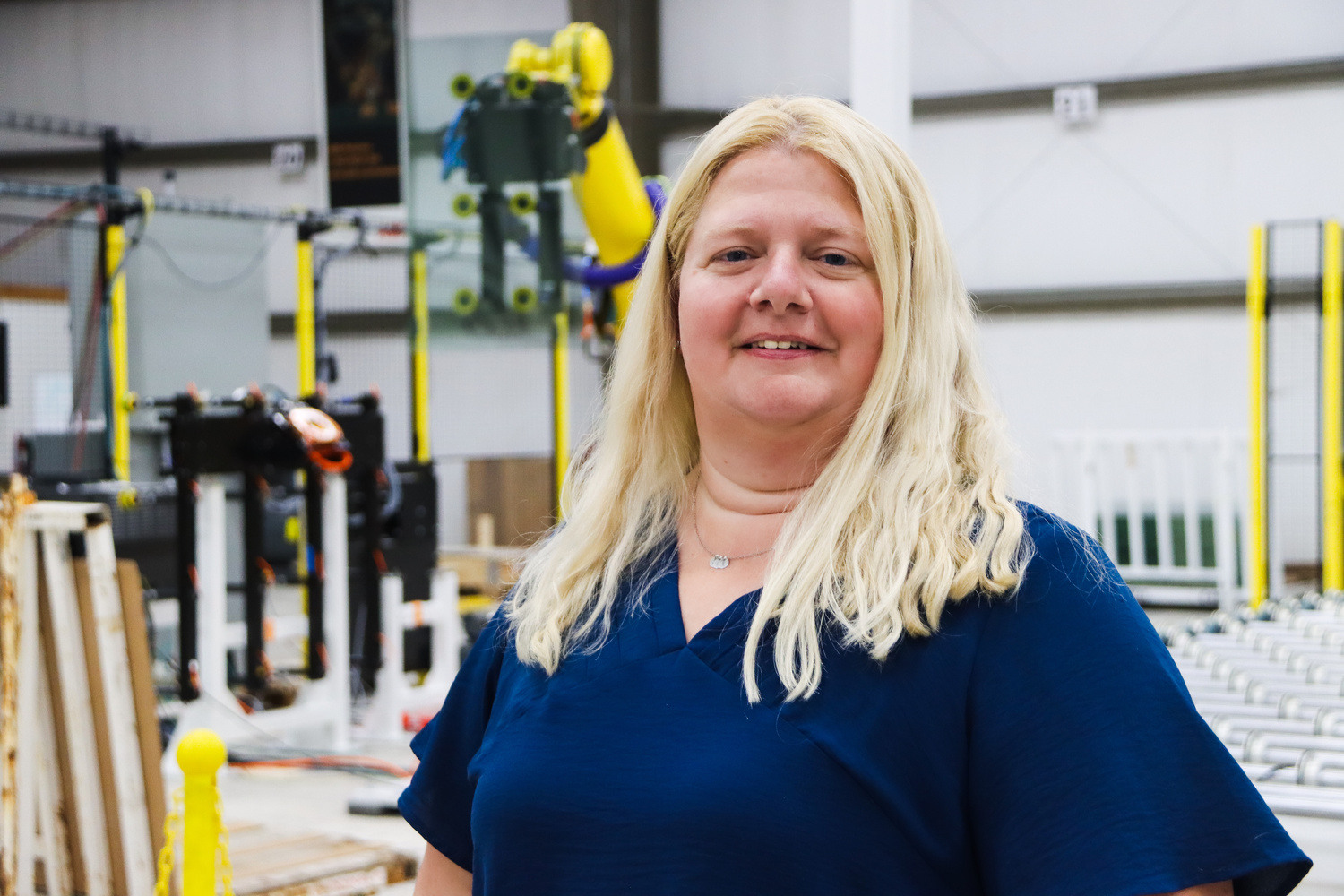
QComp Technologies Announces Company President
Katie Miner is named president of QComp Technologies, bringing expertise to lead the employee-owned company in innovative robotic solutions for complex industries.