What Is Proactive Development of Robotic Solutions?
Looking back a few years, who could have anticipated that the unemployment rate would be at historic lows and salaries would be at historic highs? While that’s generally seen as good news, it has proven to be a major challenge for manufacturers.
Manufacturing companies that manage to hire production line workers often struggle to keep them for very long, especially in positions that require dangerous and repetitive motions or monotonous tasks like picking, placing, and packaging products.
In response to lingering labor shortages, many manufacturers are scrambling to automate tasks that were once performed by humans. But designing, programming, testing, and implementing a robotic solution from scratch takes time, especially for highly complex functions. After all, there’s a reason a manufacturer had people performing those tasks in the first place – they probably didn’t think a robot could be designed to do them well enough (or that the ROI wouldn’t be worth it).
But what if those same manufacturers had taken a proactive approach to address anticipated labor shortages and other challenges? Granted, hindsight is 20/20, but there are emerging trends on the horizon, and organizations should consider developing proactive strategies to address them now rather than waiting.
What is Proactive Development in Robotic Automation?
It’s proven that automation helps reduce labor, improve uptime and quality, and enhance safety. For many industries, however, the decision to automate is a reactive one. In other words, robotic solutions are pursued in response to a problem.
Proactive development, on the other hand, is a strategic approach in which manufacturers anticipate and address market needs and pain points before they arise. This methodology involves closely monitoring industry trends and customer feedback to identify recurring challenges and emerging opportunities. This kind of proactive approach can guide the development of robotic solutions.
More often than not, however, proactive development doesn’t require building something from the ground up. Instead, the solution is often an iterative design of an existing proven technology that hasn’t been explored yet. What might that look like?
Example of Proactive Development
Our engineering team developed a robot for a consumer goods company. Initially, our task was to attach lids to pouches containing wet wipes. This required complex programming that involved vision technologies, custom tooling, and advanced capabilities for applying adhesives, positioning lids, inspections, and much more.
We know, however, that a product’s design and packaging will inevitably change. So, our engineers proactively programmed the robot with flexibility and adaptability in mind. Now, when the lid or packaging materials or dimensions get updated, or a new product SKU that requires lidding is added, the producer won’t have to invest in another robotic arm or production line; the same robot can be adapted to accommodate their needs.
Beyond lidding, our client saw an opportunity to enhance the packaging process further. They requested capabilities for case packing, where not only one but two different types of pouches could be placed into a single carton. Additionally, they saw an emerging need for high-volume packaging with bands around the pouches for bulk orders. The latest advancement involves handling bulk lids delivered in hoppers. We're developing a system to automatically sort, orient, and organize these lids to integrate them into the lidding process without manual intervention.
The customer experienced the improved quality and throughput of the lidding robot and had the foresight to consider how other processes in the production line could be automated, too. These iterations represent a shift from a single task to a comprehensive, fully automated end-to-end solution, demonstrating a proactive approach to developing and refining technologies.
Consider areas of your own production process that could benefit from automation. Have you assumed that robotic technologies don’t exist for a specific material handling challenge? Truth is, there may not be a robot on the market that fits your needs… yet. But with a proactive mindset and the right integrator, there’s a good chance that an existing technology can be adapted to meet your needs. It’s worth exploring the possibilities.
The Benefits of Proactive Automation Development
In the end, a proactive approach benefits both the customer and the robotics company. By expanding existing solutions, the robotics company builds on proven success and significantly reduces development time, costs, and risk. Those savings are passed on to the customer. Once a solution is perfected and standardized, it can be replicated for other related tasks with minor adaptations, significantly lowering the cost per unit.
At QComp Technologies, we tackle highly complex material handling challenges every day, from glass handling and consumer goods to food handling and more. We invite you to connect with us to discuss how our forward-thinking solutions can meet your current challenges and prepare you for future opportunities.
Contact us today to explore the possibilities.
Share this
You May Also Like

Common Cobot Safety Risks & Prevention Tips
What is the difference between a cobot vs. robot, and what safety features need to be implemented to prevent injuries? Learn about cobot safety tips.
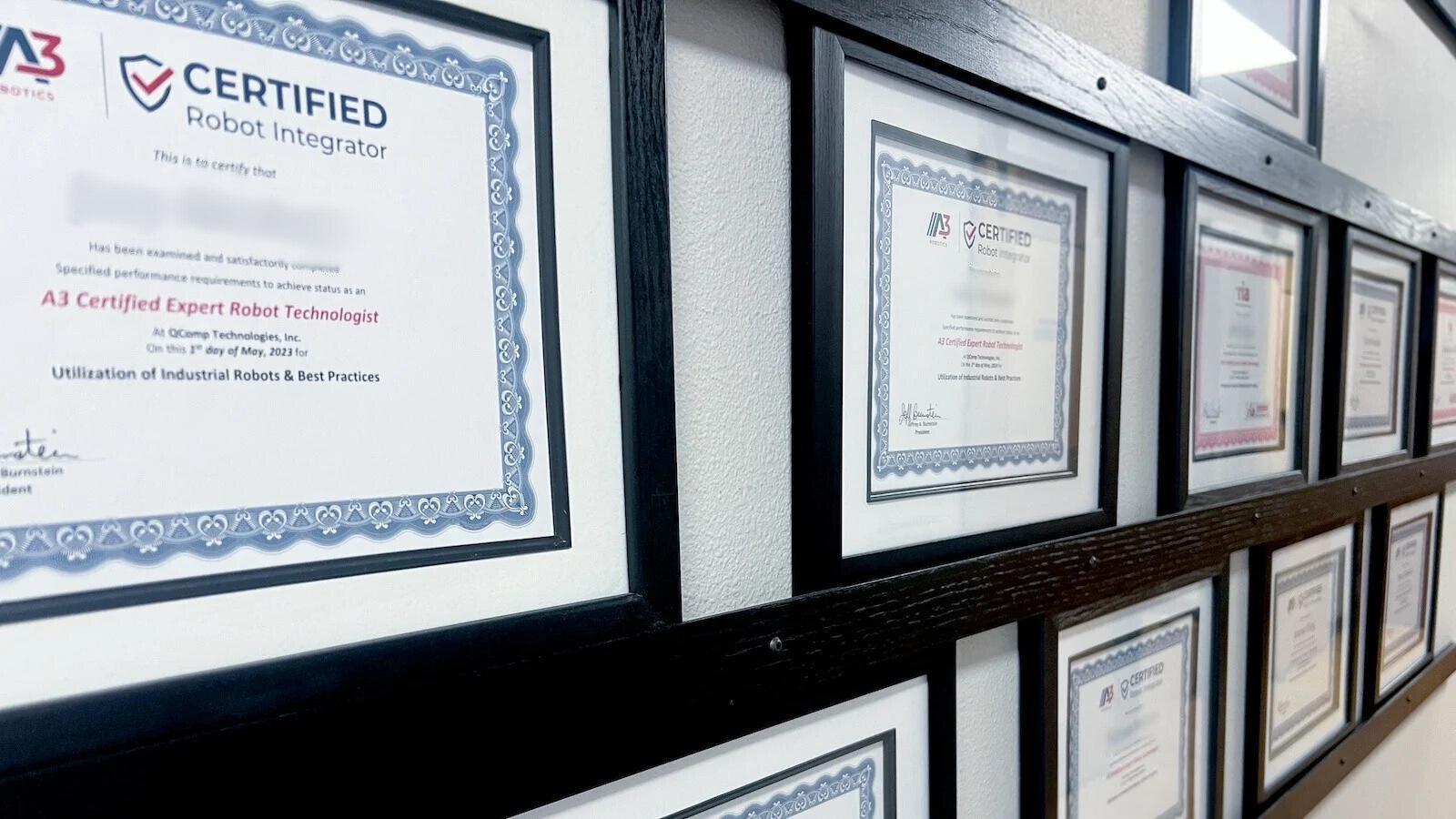
Why A3 Safety Certification Matters for Robotic Integrations
What is A3 safety certification? Explore the benefits and importance of The Association for Advancing Automation (A3) certification for robotic integrators.
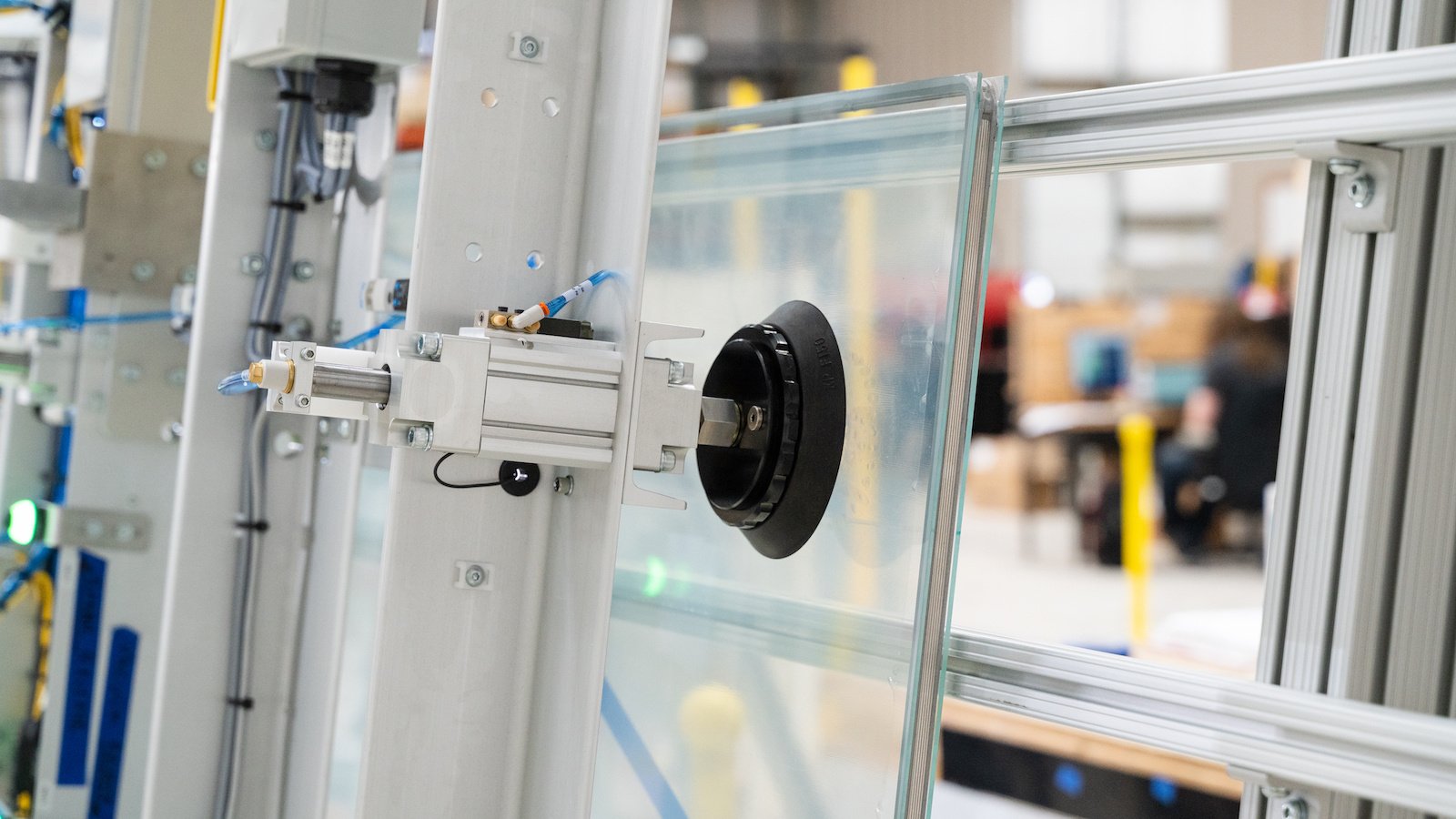
Overcoming the Limitations of Robotic Arms with Vacuum Grippers
Learn how robotic engineers tackle complex material handling challenges by overcoming limitations of vacuum grippers. Discover innovative solutions for automated processes.